The 2013 iteration of California’s Title 24 energy standards, which came into effect last July, effectively raises the bar on the energy performance of buildings. One aspect of their thermal performance which now comes under the microscope in terms of obtaining the building’s final permit and Certificate of Occupancy is air infiltration. And can lights, while aesthetically pleasing, present certain real challenges from an energy performance perspective.

Recessed lights add elegant beauty to this minimalist bathroom, a beauty that comes with an energy price tag.
Recessed Can Lights: The Beauty And The Beast Also known as “can lights” or “downlights”, recessed lighting lends an uncluttered look that provides light without taking up headroom or ceiling space. Recessed lights are often used to highlight wall features or to provide focused overhead lighting for reading or working. They can be used to increase the amount of light in a room, highlight artwork or other special features, and open up spaces so they look and feel bigger. But if we look at a can light with an infrared camera we’ll usually see evidence of air leaks at the perimeter of each fixture. In most cases, these innocent-looking circles are actually holes in the ceiling element of the building envelope.

Infrared images showing heat leakage through the insulation above an IC rated, airtight recessed light.
Recessed Lighting: The Problem The building envelope is a continuous layer separating the interior from the exterior. The closer the building envelope is to an uninterrupted whole, the more efficient the building will be. Recessed lights arose as an alternative to their surface-mounted predecessor – with the trade-off in terms of energy performance being that we’ve now punched a hole through the building enclosure. Our neat, uncluttered interior lighting solution comes at the cost of a substantial amount of conditioned air leakage for that appearance. The fixtures penetrate the air barrier and almost always make the house less efficient. With the new Title-24 regulations, recessed lights are required to have airtight housings (called AT-rated). They achieve this by implementing weather-stripping at their perimeter, at the trim. But so-called “airtight” recessed can lights are not literally airtight, but simply leak less air than conventional recessed cans. Not only do even AT-rated recessed can lights leak some air, but the hot lamps inside them also make the situation worse, turning the holes in the building envelope into small chimneys. The heat source accelerates the stack effect, accelerating the flow of air. Still worse, each fixture takes up roughly the area of a quart-sized paint can, taking up room in the ceiling that would serve a thermally better purpose filled with insulation.
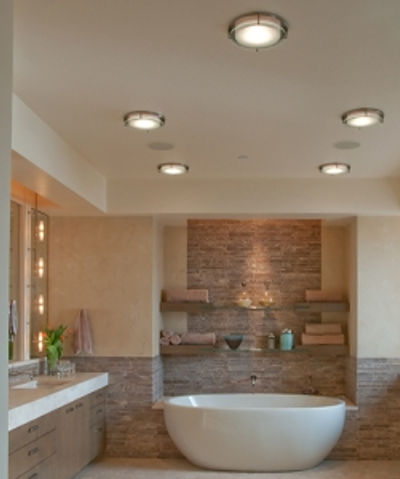
New product lines of surface-mounted lighting present an attractive – cost-wise, energy-wise, and aesthetically-wise – alternative to recessed cans.
What To Do? Despite the increased labor to make them 100% airtight and the potential costs for retesting until we pass the energy audit at permit final, if we do insist on using recessed lights, we may need to consider designing them into either secondary dropped soffits or soffit boxes, thus keeping the light source elegantly out-of-sight without punching holes in the thermal envelope. The problem with this approach is that, while potentially sculpturally pleasing, we’ve essentially converted a relatively affordable light source into a disproportionately expensive and thus inelegant lighting strategy from a costs-benefits perspective. The most cost effective and easiest solution may be to exorcize recessed light cans from the designer’s mental quiver of design tools. Once we begin move away from recessed cans, we can also move away from their limitations e.g. the fact that they are fixed in one place, and either unidirectional or with only a limited range of direction. There are literally dozens of ways to elegantly light a space other than by gouging a hole through the air barrier.
Comments